高级生产排程如何实现
高级生产排程是一种复杂的计划过程,旨在优化生产资源的使用,确保生产活动按时、按质完成。它涉及多个步骤和考虑因素,以下是实现高级生产排程的关键步骤:
需求预测与订单管理
准确预测:通过市场调研、历史销售数据、行业趋势等多维度信息,运用统计模型或机器学习算法进行精确预测。
订单管理:建立完善的订单管理系统,实时跟踪订单状态,包括接收、审核、确认、变更及取消等环节,确保订单信息的准确性和及时性。
产能规划与资源评估
产能分析:根据设备性能、人员技能、工作时间等因素,计算生产线的最大产出能力,并考虑维护、故障等因素对产能的影响。
资源评估:全面盘点原材料、零部件、能源等生产资源,确保其供应充足且质量合格,同时评估人力资源配置是否合理,是否需要培训或招聘新员工。
生产计划制定
主生产计划(MPS):基于需求预测和订单情况,制定未来一段时间内的生产总量计划,明确各产品的生产数量和交付时间。
物料需求计划(MRP):根据MPS和产品结构(BOM),计算出所需原材料和零部件的具体需求量和到货时间,生成采购计划和生产指令。
排程优化
约束条件设定:考虑设备能力限制、工艺要求、换线时间、库存成本等多种约束条件,构建数学模型或使用专业软件进行模拟仿真。
算法应用:利用线性规划、整数规划、遗传算法、启发式算法等方法,对生产任务进行最优分配和排序,以最小化生产周期、最大化产出率、降低库存成本等目标。
动态调整与执行监控
实时反馈机制:建立生产现场的信息采集系统,实时收集设备运行状态、物料消耗、产品质量等数据,及时发现并解决问题。
动态调整:根据实际生产进度与计划的偏差,快速调整生产计划和排程,如重新分配任务、调整生产顺序、增加加班等。
绩效评估:定期对生产计划执行情况进行评估,分析差异原因,持续改进排程策略和方法。
协同与沟通
跨部门协作:加强生产、采购、销售、仓库等部门之间的信息共享和协同工作,确保生产计划与其他业务环节无缝对接。
供应商管理:与关键供应商建立长期合作关系,共同应对供应链风险,确保原材料供应的稳定性和准时性。
综上所述,实现高级生产排程需要综合运用多种技术和管理手段,从需求预测到生产执行全过程进行精细化管理,不断优化资源配置,提高生产效率和客户满意度。
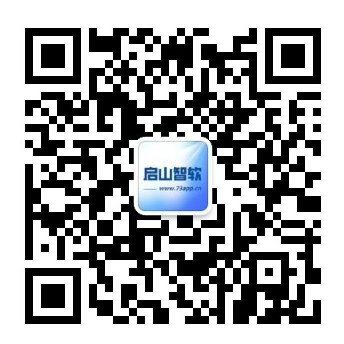