自动生产排程系统的工作原理
排程系统的工作原理通常涉及以下几个主要方面:
一、数据收集与输入
订单信息:包括订单数量、交货日期、产品规格、优先级等。这些信息是排程的基本依据,决定了生产任务的紧迫性和重要性。
资源信息:
设备信息:如设备类型、设备数量、设备性能参数(生产速度、加工精度等)、设备维护计划等。了解设备的能力和可用性对于合理分配生产任务至关重要。
人员信息:人员技能水平、工作时间、排班情况等。不同的人员具备不同的技能,能够操作不同的设备或执行特定的生产任务。
原材料信息:原材料库存水平、供应周期、质量状况等。确保原材料的及时供应是顺利进行生产的前提。
二、约束条件设定
时间约束:
订单交货日期:这是最关键的时间约束,排程系统必须确保生产任务在规定的交货日期前完成。
设备维护时间:设备需要定期进行维护保养,在排程时要避开设备维护时间段,以免影响生产进度。
工作时间:考虑人员的工作时间和休息时间,以及工厂的运营时间,合理安排生产任务。
资源约束:
设备能力约束:不同设备的生产能力有限,不能超过其最大负荷。例如,一台机器每小时只能生产一定数量的产品,排程时不能安排超过其能力的生产任务。
人员技能约束:某些生产任务需要特定技能的人员来执行,排程系统要确保分配给合适的人员。
原材料供应约束:确保在生产过程中有足够的原材料供应,避免因原材料短缺而导致生产中断。
三、算法与优化
排程算法选择:
常见的排程算法有遗传算法、模拟退火算法、禁忌搜索算法等。这些算法通过不同的方式对生产任务进行排序和分配,以找到最优或近似最优的排程方案。
算法的选择取决于生产环境的复杂性、问题规模、计算时间要求等因素。
优化目标设定:
通常的优化目标包括最小化生产周期、最大化设备利用率、最小化库存水平、最大化客户满意度等。排程系统根据设定的优化目标,在满足约束条件的前提下,寻找最佳的生产安排。
可以是单一目标优化,也可以是多目标优化,需要根据企业的实际需求进行权衡和选择。
四、排程生成与调整
初始排程生成:
基于收集的数据和设定的约束条件,排程系统运用选定的算法生成初始的生产排程。这个排程方案会给出每个生产任务的开始时间、结束时间、分配的设备和人员等信息。
排程调整:
在实际生产过程中,可能会出现各种变化和干扰因素,如订单变更、设备故障、人员缺勤等。排程系统需要能够及时响应这些变化,对排程进行调整。
调整可以是局部的,只针对受影响的生产任务进行重新安排;也可以是全局的,对整个排程进行重新优化。
五、结果输出与反馈
排程结果输出:
排程系统将生成的排程方案以直观的方式呈现给用户,如甘特图、报表等。用户可以查看每个生产任务的详细信息,了解生产进度和资源分配情况。
反馈与改进:
用户可以根据实际情况对排程结果进行反馈,提出修改意见或建议。排程系统根据反馈信息进行进一步的优化和调整,不断提高排程的准确性和合理性。
同时,排程系统可以通过对历史数据的分析和学习,不断改进算法和优化策略,以适应不同的生产环境和需求变化。
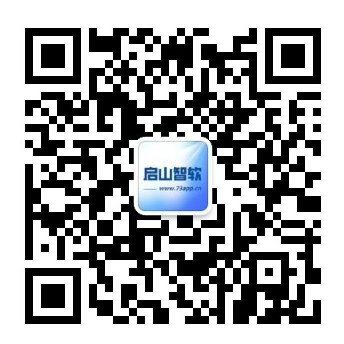